Plastic Flat Yarn Making Machine
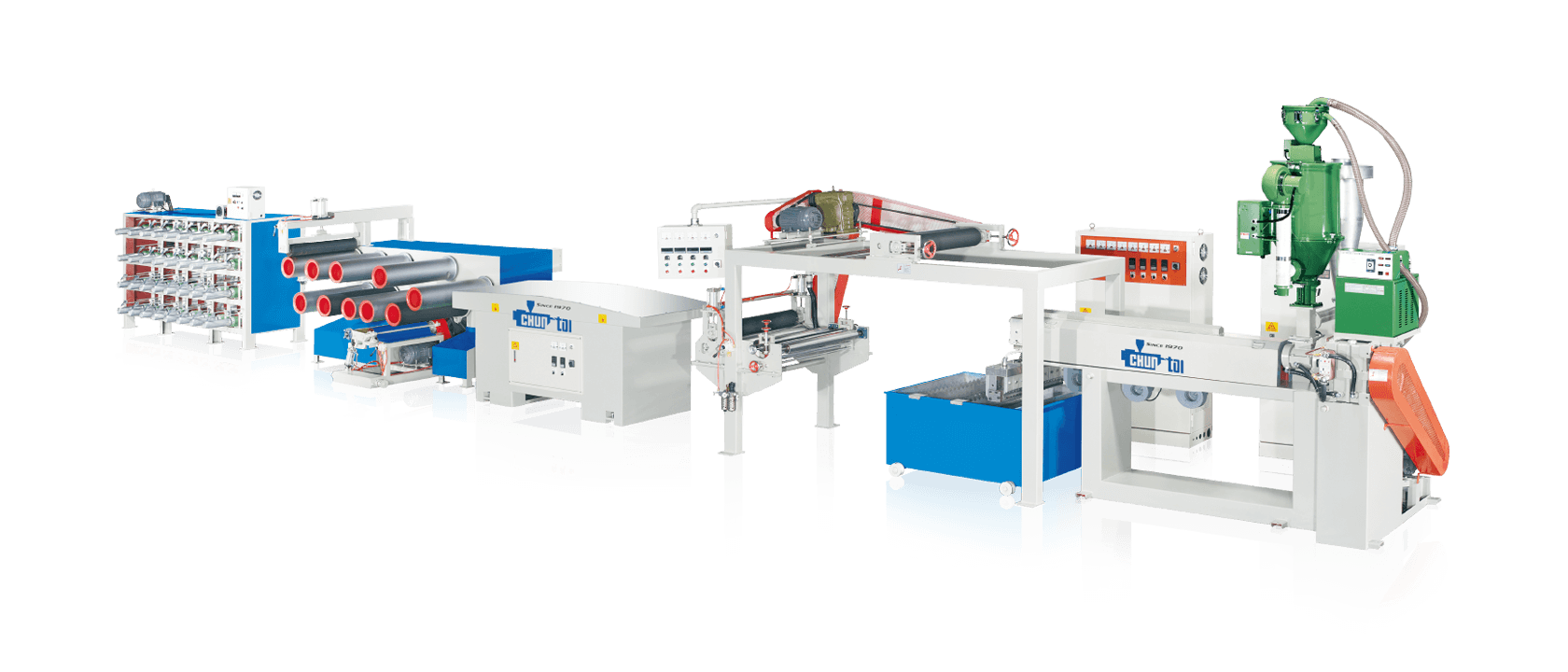
Versatile Extrusion Line for High-Strength Flat Yarns
Product Overview
The Plastic Flat Yarn Making Machine is an advanced extrusion solution tailored for producing high-quality flat tapes commonly used in woven sacks, FIBCs (jumbo bags), and construction mesh. It supports both virgin and recycled materials, giving manufacturers the flexibility to balance cost and quality. With precise control over yarn width, thickness, and stretching ratio, this machine is ideal for efficient and consistent production across various industrial applications.
Key Features
- Adjustable Yarn Dimensions:
Easily customize tape width and thickness to meet diverse product requirements, including cement bags and protective netting. - Precision Stretching with Temperature Control:
Fine-tune the stretching speed and heat settings to ensure consistent tensile strength and stability during production. - Single-Axis Winder:
Designed for simplicity and reliability, this take-up system ensures smooth operation and is easy to maintain—ideal for long production runs. - Seamless Integration with Downstream Equipment:
Fully compatible with automatic weaving lines, helping streamline production and reduce intermediate handling.
Application Industries
- Packaging – Woven bags, jumbo bags, rice sacks, feed sacks
- Construction – Cement bags, building reinforcement mesh
- Agriculture & Industry – Shade nets, protective fencing, separation nets
Technical Specifications
Item | Description |
---|---|
Yarn Width and Thickness | Customizable to meet specific production needs |
Stretching Ratio | Adjustable, supported by a precise thermal control module |
Winding System | Single-axis, easy to operate and maintain |
Tension Control | Manual adjustment available |
Line Compatibility | Integrates with downstream woven bag production lines |
Die Head and Filter | Easy to access; maintenance frequency depends on material type and cleanliness |
FAQ
- Q1: How can yarn breakage during stretching be avoided?
A1: Breakage is often caused by unstable material formulations or contamination. It’s recommended to use clean, compatible raw materials and apply effective pre-filtration. - Q2: How often should the die head or filter screen be replaced?
A2: Replacement frequency depends on the material’s cleanliness. When using recycled material, regular inspection and timely replacement are essential to maintain product quality. - Q3: Can the machine produce different yarn sizes?
A3: Yes. By adjusting the die head and processing parameters, the machine can produce various flat yarn sizes without requiring extensive tooling changes.